为了保证铸铁工作台的铸型表面粗糙度符合要求,对铸型要做打磨处理,铁液凝固时间长,铁液与型、芯相触的时间较长,为了防止铸铁工作台的铸件产生粘砂、夹砂、砂眼等缺陷,在型、芯转角处及铸铁工作台下部平面部位使用锆英粉醇基快干涂料,其他部位使用自制的水基涂料,涂料层厚度取0.6~1.5 mm。机械加工余量:上部为+20 mm,下部+20、侧部均为+15 mm。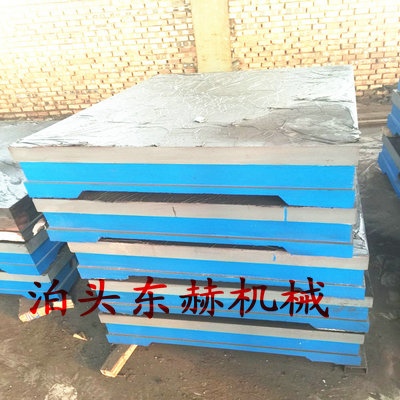
1.型、芯工艺。为了使型、芯的尺寸精度、表面粗糙度达到要求,全部采用冷硬呋喃树脂砂造型、制芯。型砂配比为:树脂加入量为原砂的1.2%~1.4%,固化剂加入量为树脂加入量的40%,24 h抗拉强度大于0.8 MPa。铸铁工作台的大平面是其重要工作面,质量要求严格,铸造工艺方案应该优先考虑将大平面放置在浇注位置的下方,避免产生砂眼、气孔等铸造缺陷。铸铁工作台的结构为圆形规则体,适合采用组芯成型,铸铁工作台大平面由刮板形成,此工艺将节省可观的模型制作费用,其余由盖芯和中间芯形成,缩尺取8/1000。
2.浇注系统。因铸铁工作台外轮廓尺寸较大,铁液从平台外周引入,铁液流至中心的行程长,因此要求浇注时铁液要大流量快速充型,避免出现冷隔、涂料脱落及氧化夹渣等缺陷。浇注系统设计成底注缓冲阶梯、串联环形半开放式浇注系统,铁液从底部平稳有序地充满型腔,有利于排气、排渣。浇注系统各单元比(经修正) 取,F直∶F横∶F内=1.12∶1.43∶1。浇注系统由浇口箱、2个100直浇道、1个80环形横浇道,20个;30分散布置内浇道组成。内浇道尺寸的确定要保证先于铸件凝固,充分利于石墨化自补缩作用。
3.铸铁工作台铸件冒口的设计。由于此铸件较大,壁厚比较均匀,因此不放置补缩冒口,只设置28个140出气冒口,辅助浇口补充铸件液态收缩量,排除上部有杂质的铁液。主要由浇注系统补充液态收缩不足量,凝固过程利用石墨化膨胀进行自补缩。